FAQ
WHY IS THE PERMITTING PROCESS SO IMPORTANT?
Many people think the reason the government wants you to get a permit is so they can raise your taxes. While that may be true in some cases, the real benefit to following the local residential permitting process is for the protection of the homeowner.
The governing jurisdiction has developed and agreed on a set of standards for the community. These are typically divided into zoning and building. Zoning has to do with the setbacks from lot lines, coverage of the non-porous items, such as buildings, driveways, sidewalks, etc., height restrictions, use, and similar items. The building standards are typically adopted, often with modifications, from international
authorities, specifically the International Residential Code (IRC). These are locally referred to as the Building Code Following this Building Code assures that construction in the community is built to at least these minimum standards.
The permitting process helps to ensure that construction and building modifications comply with the local Building Code, and therefore meet certain minimum standards for size, functionality, safety, and integrity.
While the permitting process can seem bureaucratic in some cases, it is a necessary step in the orderly development of a community, and helps to ensure the safety of its residents and guests. Whether we work on a project with a permit or not, we do our work in accordance with the applicable code requirements. No shortcuts here.
WHAT IS THE DIFFERENCE BETWEEN SANDED AND UNSANDED GROUT, WHEN SHOULD EACH BE USED?
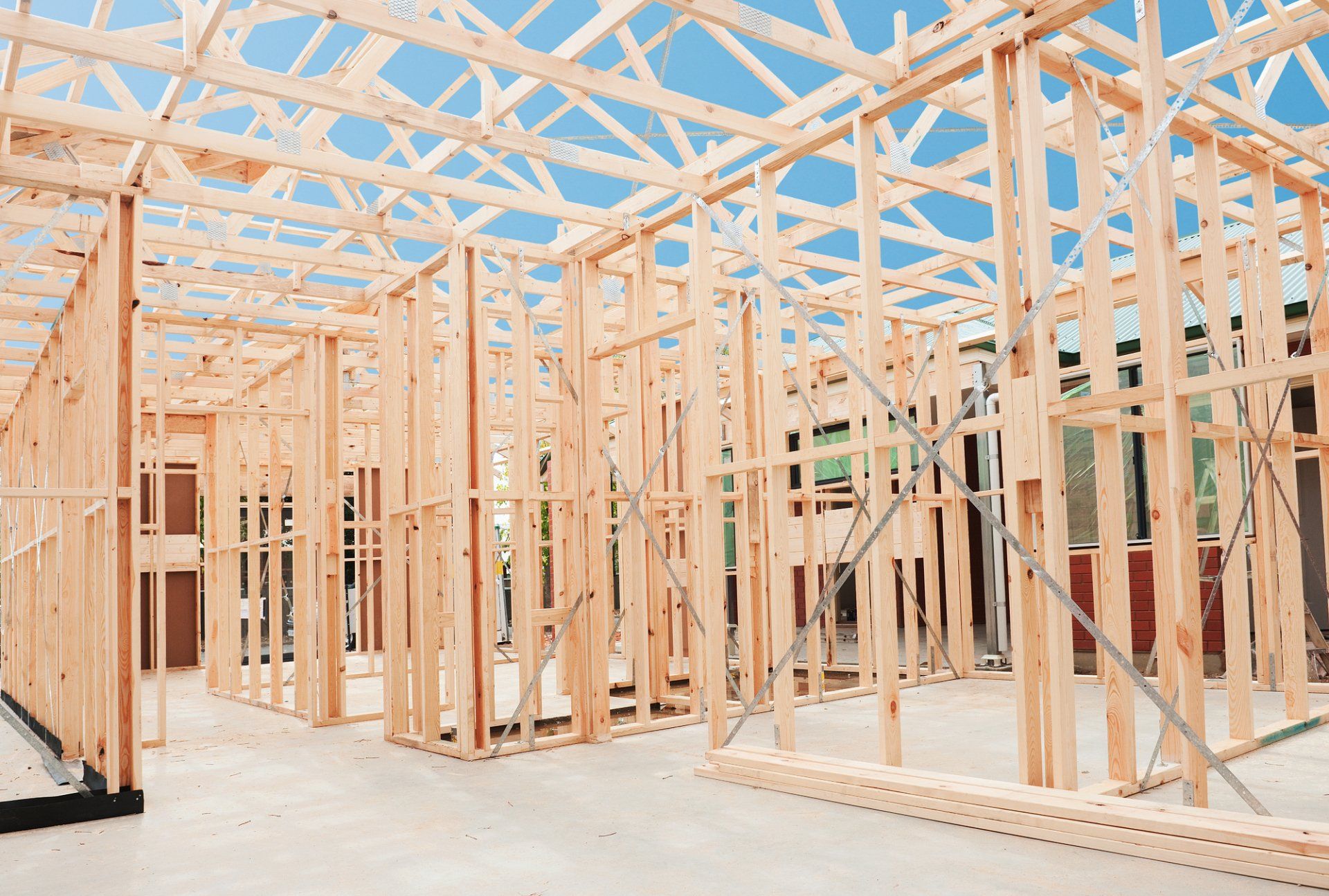
WHAT IS THE DIFFERENCE BETWEEN A TEAR-OFF AND A LAYOVER?
WHAT'S THE BEST MATERIAL FOR BLOCKING SOUND UNDERNEATH HARDWOOD FLOORS?
We're renovating the upstairs unit and putting in hardwood floors. We're concerned that the new floors will be very noisy for us as the downstairs tenants. Who makes the best underlayment for blocking sound?
You bring up a very interesting challenge. We are working on hardwood as well as tile floors (hard floor surfaces) in both single family, as well as condos in the Chicago area.
We break the appropriate answer into three scenarios:
- Single Family (you can do what you want)
- Low density multi family with no condo association rules (you can provide sound attenuation for the benefit of your neighbors because you want to)
- High density multi family with condo association rules (you must provide sound attenuation typically conforming to specific STC or IIC ratings as approved by the association)
First let’s start with a couple of industry definitions:
Sound Transmission Class (or STC) is an integer rating of how well a building partition attenuates airborne sound. In the USA, it is widely used to rate interior partitions, ceilings/floors, doors, windows and exterior wall configurations (see ASTM International Classification E413 and E90).
IIC stands for impact insulation class. Acoustic labs conduct the IIC test using a tapping machine with steel faced hammers. These hammers strike a test floor material generating sounds between 125 to 4,000 Hz. The impact creates vibrations that travel through the floor into the receiving side (the room below). Source: http://isostore.com/comparing-sound-ratings/
What really matters:
Some of the underlayment systems at big-box stores have high STC or IIC ratings, and it may seem a good choice, but what really matters is the assembly, not the individual underlayment choice. The assembly is the collection of the individual components as they work together in a system. This is key. Testing a simple piece of underlayment doesn't tell you much. It is how the sound is transmitted through the hardwood flooring subfloor underlayment what is underneath that matters, and for a valid test, it must be together.
With Scenario 1, in a single family residence, you may wish to have some kind of sound attenuation so you don't hear people walking above you, and the solution will depend on how much extra money you wish to spend, and how much you want to isolate the noise. Any dampening underlayment will deaden or attenuate the sound to some degree. Advice: get a sample of the hardwood, and underlayment, place it on the floor you wish to cover and see how it performs. Have someone walk on it with hard heels, or drop marbles on it, whatever your lifestyle may be, and see if it is good enough for you.
Scenario 2: in a multi-family not requiring a specific rating, you can do the same as Scenario 1 above. Or, if you want to or can spend the money to increase the sound attenuation, you can try 1/4" cork, a rubber mat system, a closed cell underlayment, etc. You can also take a look at the playbook of a large multi-family scenario. Some have hired Acoustic Sound Engineers to do testing for them and give them
recommendations as to the approved assembly.
Scenario 3: large multi family with rules...Many large condos have specific recommendations and/or specifications on what may and may not be used for hard surface flooring. For example one downtown Chicago condo building on Dearborn wants 1/4" cork under an engineered floor, but for a 3/4" standard hardwood floor, additionally requires a 3/4" underlayment as a nailing receiver for the hardwood floor fasteners. This obviously increases the floor height between 1/4" to 1'. Another large condo building on Sheridan Road in Chicago requires specific IIC ratings and hired a Sound Engineering firm to come up with recommendations. I will share them below.
For Hardwood flooring, adhere the underlayment to the slab with adhesive as recommended by the manufacturer. Install two layers of 1/2" OSB or plywood over the underlayment that are adhesively bonded together. Orient the nailing layers perpendicular to each other. Install the hardwood flooring by nailing/stapling into the plywood layers. Select 1 1/4" max nail length (can't penetrate the underlayment). As for the underlayment, the unit owner may choose one of the products that achieve an acoustical rating of at least AIIC 52. Fintech AcoustiTech 7000 (7mm felt type mat), Pliteq Geniemat RST10 (10mm recycled rubber mat), AcoustiCork S130 (13 mm cork)
Note that the rules for Engineered and Laminate Wood Flooring will probably be different, and may be floated. The rules for ceramic/porcelain are also different.
I bet you've never seen this before
Here is what we found inside one of our customer's cold water supply pipe. What is it? Mineral deposits. Most areas of the country have dissolved solids that come from both municipal and well water. After many years the minerals can cling first to the pipes then to more minerals eventually clogging the pipes to a trickle. Biggest clue: low water pressure, especially on the hot side.
If you have low water pressure, here's what to do: if it's just at one location, for example a faucet, likely it's just the aerator - that's the filtering end of the spigot of the faucet where the water comes out. Almost all unscrew and can either be cleaned or replaced.
If that doesn't fix the problem, it could be sediment or mineral build up near the valve or supply line which can often be taken apart and cleaned.
Finally, if the problem persists, or it's widespread in your home, likely the pipes are clogged inside (worse than the picture) and it's time for replacement. We call it re-piping.